金属粉末射出成形 MIM (Metal Injection Molding)とは?
金属射出成形は、別名MIM(Metal Injection Molding)とも呼ばれており、プラスチック射出成形と金属粉末冶金の技術を応用して複雑形状の金属部品をニアネットシェイプ(Near Net Shape)の状態で製造する技術のことを言います。10ミクロンレベルの微細な金属粉末を原料として、射出成形をするため、チタンやステンレスなど加工難易度が高い材料においても複雑形状に加工をすることができます。近年では自動車をはじめ、精密機械・電気機器・通信機器・医療機器の部品を製造する際に使用できる可能性があるということで、注目されている加工方法の1つであります。
特徴
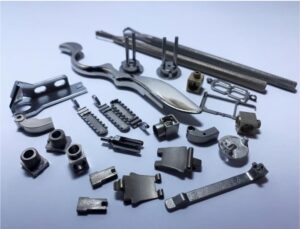
メリット(従来工法と比較して)
金属部品の製造にはダイキャストやロストワックスなどの鋳造、鍛造、機械加工、プレス加工など様々なものがあります。 これらの工法とは異なりMIMは、原料に金属粉末を使用し、つなぎ(バインダー)を加えて射出成形した後、脱脂・燃結することで高精度な金属部品をつくる技術です。 量産性に優れており、切削加工などの後加工が少なく、自由に配合した材料を使用することができるなど、従来工法と比較して際立った特徴があります。つまりMIMは「量産性の高さ」・「後処理の容易性」・「機械的特性に強さ」・「材料の自由度の高さ」でメリットが発揮でき、信頼性が必要な難加工材料、複雑小物の高精度部品に適した工法と言えます。
難加工材でも複雑形状に加工することができる
切削やプレス加工では製造が難しい、チタンやタングステンなどの難加工材での生産も可能です。超硬金属・チタン・ステンレス・タングステンなどの切削加工が困難な、いわゆる難加工材と呼ばれる材料でも、材料ロスの発生が無く製作することができます。切削加工では素材を削る必要がありますが、金属粉末射出成形であれば、切り粉が発生しないためその分材料効率が良いと言えます。
高精度の加工ができる
鋳造の中でも比較的精度の高いロストワックスでも一般公差が±1%であるため、金属粉末射出成形は非常に高い精度で加工することができると言えます。高精度金型による比較的複雑形状なニアネットシェイプが製造可能となります。切削加工などの後加工を必要としない場合が多い。部品の一体化などの提案もしやすい。
大量生産が可能
金属粉末射出成形(MIM)は金型を使った製法であるため、大量生産が可能です。難加工材にも対応できるため、1つの部品を製作するのに多くの時間がかかっていたようなものでも、比較的短時間で製作することができます。金型による製造のため、大量生産に優れており、コストダウンにつながることが多い。
コストダウンの実現
金属粉末射出成形は、中間の加工工程を短縮することができるのでコストダウンに繋がります。複雑形状であればあるほど加工工程が増えるため、金属粉末射出成形法によるメリットを大きくすることができます。ニアネットシェイプの三次元形状、接合による部品の複合化、量産性が高いといったMIMの特徴を組合せることにより、後加工が省略でき、部品点数の削減、組付け機器の小型化などにつなげることができ、トータルコストの面で優れています。
デメリット
大型形状の製造は不向きで、金型イニシャル費用がかかります。
従来工法とMIMの違い
製造コストの 安価性 |
量産性の 高さ |
後処理の 容易性 |
機械的特性の 強さ |
寸法精度の 高さ |
材料の自由度 の高さ |
形状の自由度 の高さ |
|
MIM | ○ | ◎ | ◎ | ◎ | ○ | ◎ | ○ |
切削加工 | ×× | × | ◎ | ◎ | ◎ | △ | △ |
ダイキャスト法 | ◎ | ◎ | ○ | ×× | △ | × | ○ |
ロストワックス法 | ○ | × | △ | ○ | △ | ○ | ◎ |
鋳造法 | ○ | ○ | △ | × | △ | × | ○ |
鍛造法 | ○ | ○ | ○ | ◎ | × | △ | × |
圧粉焼結法 | ○ | ◎ | △ | × | ○ | ◎ | ×× |
MIM製法は他の加工方法と比較してみると著しく劣っているものが少なく、量産性の高さや後処理の容易さはもちろん、コストや精度など全体的にバランスが良いとも言えます。ダイキャスト法も比較的優秀ではありますが、機械的特性や材料の自由度が低く、使いたい原料によっては加工に不向きな場合もあります。また、切削加工は精度が高いもののコストがかかるのがデメリットです。鍛造法や圧粉焼結法は形状の自由度が低いため、複雑な製品などにはあまり向きません。MIM以外の製法は大きなデメリットがあるのに対し、MIMは原材料が高いという点以外はデメリットがないとも言えます。
鋳造・鍛造とMIMの違いについて
鋳造は金型に溶かした金属を流し込んだ後、冷やして固める手法、また鍛造はインゴットを金型で挟み込み、プレスして引き延ばすことで形作る手法です。鋳造のデメリットは、金属の塊(インゴット)を金型に流し込むためには溶かさないといけないということで、時には流し込んだ時に ”巣” と呼ばれる空気穴みたなものが製品の中にできてしまうこともあります。しかし、鋳造はどうしても製品精度がよくありません。ロストワックスと呼ばれる手法は比較的高精度の鋳造法ですが、それでも±0.1mm以上の誤差が出ることはよくあります。ここで、鋳造・鍛造と金属粉末射出成形を比較すると、鋳造と大きく異なる点は金属を溶融させないことです。金属粉末射出成形(MIM)は、金属の粉末と樹脂を混ぜて金型の中に射出成型します。金属粉末のみであれば、固めることができないため、つなぎの役割を担う樹脂を金属粉末に混ぜて射出成形し、成形体を脱脂・焼結をすることで加工をします。また、金属粉末射出成型は高精度ですし、ロットごとの品質のばらつきも少ないメリットがあります。
焼結合金とMIMの違い
射出成型という技法はプラスチック製品の量産などによく使われており、溶かした樹脂を金型に射出充填することで製品を作るので、形状の自由度が非常に高いのが特徴です。その利点を生かして、難加工剤の成型に使ったのが金属粉末射出成型です。金属粉末射出成型を簡単に言えば、金属の粉を金型に押し込んだ後に焼いて固める手法です。金属の粉を焼き固める焼結と比較すると、焼結合金は粉末をプレスして成形するのに対し、MIMは金型での射出成形になるのでより複雑な3次元形状を製造でき、精度が高いと言えます。具体的に説明すると、MIMは金属の粉末と樹脂を混ぜて金型の中に射出成型します。金属の粉末だけでは、固まらないので ”つなぎ” の役割を果たす樹脂を混ぜているのです。一度、金型の中に充填した金属粉末と樹脂の混合物に脱脂処理を加えて樹脂を取り除きます。この段階では、まだ柔らかいので熱を加えて焼結すると、高精度な金属部品が出来上がります。
チタンとステンレスのMIM加工について
難溶性のチタンやステンレスにも利用できる
錆びない、軽い、高強度ということで使用される機会が増えているチタンや昔から広く使われているステンレスは難削材で、加工性が悪いと言われています。専門の加工技術が求められ、鋳造するのも難しく、特にチタンは融点が1,670℃と非常に高いです。鋳造に使われる型(鋳型)の温度が幅はありますが、だいたい800℃くらいです。チタンを溶かして流し込むと、鋳型と接触したところから瞬間的に凝固してしまうので型の中を完全に隙間なく溶けたチタンで埋め込むのが難しいのです。金属粉末射出成型の場合、高温にして溶かす必要がないので、鋳造ほど隙間の心配はいりません。
難削材のチタン・ステンレス加工に威力を発揮する
MIMはミリオーダーで三次元複雑形状の製造を可能にした次世代の微細成形加工をになう技術です。今後は医療用器具や電子機器など、マイクロ部品の製造技術として小型化、複雑形状にも対応できることから幅広い分野での活躍が期待されております。特に医療用の部品はチタンが多く、切削するには小さすぎるものがあり、製品形状によってはチタンのような難削材だと切削加工で形をつくることが難しいことが多々あります。この場合MIMを利用すれば問題なく製作することが可能です。また、チタンやステンレスなどの難削製品を大量生産でき、薄さと厚さ関係なく製作できます。すごく小さいものや、薄いもの、形状が複雑なものほど有用性が高いです。最終的には、研磨やラップ(磨き)などが必要になることもありますが、大幅に機械加工を減らすことができるMIMは今後も広く使われると期待されております。
TECH-JOURNEYのMIMについて
金属粉末射出成形法(Metal Injection Molding)とは、粉末冶金(焼結)技術とプラスチック射出成形技術を融合した、新しい加工技術。微細金属粉末と特殊バインダーを混合し、混練した原料を任意の形状に成型、脱脂工程、焼結工程を経て金属部品として完成させます。光通信部品や自動車・時計部品をはじめ、HDD部品、熱処理用治具などで利用。設計の自由度が高く、工程圧縮化や一体化を実現できます。近年では情報機器、電子機器、医療機器をはじめとする製品の小型化・高性能化によって部品の高精度化・複雑形状化の流れがますます進んでいる中、MIMを利用すれば、従来困難だったコンパクトかつ複雑形状の部品を、高精度・高密度で大量生産できると注目されている加工方法の1つであります。岐阜精器工業のMIM加工の技術は、長年培ってきた真空熱処理をベースにした高い技術力です。粉末材料の開発から、複雑小物部品・難加工金属への適用、高密度な 部品の提供や大型部品の製作など、独自の技術力で高度なニーズに対応します。また、量産性に優れており、弊社では月産1,000個~100万個まで対応可能です。重量としては0.05gから50g程度までの部品に最も適しており、100g程度までは量産可能です。小ロットから量産まで、金型製作から責任を持って承っており、材料選定・コストダウン・工法変換・軽量化・品質向上・納期短縮でお困り事がございましたら、お気軽にお問い合わせ・ご相談ください。
岐阜精器工業のMIMの海外調達について
創業50年の金属加工の技術・知識および協力ネットワークを活かして、海外生産・調達をトータルサポート致します!
岐阜精器工業は中国で最も技術力の高いMIMメーカと提携し、製造・販売を行っています。お客様のご依頼内容に応じて、提携先から最適な工場を選定、精度・品質レベルの高い製造工場で部品を加工し、弊社の品質検査を得て日本に出荷いたします。部品調達を中国調達に切り替えるとコストダウンを実現することができます。弊社の場合、金型費最大50%、製品単価最大30%までコストダウンが可能になります。高品質・高精度・低コストのMIM部品をお求めの場合はまず弊社にご相談ください。また、海外の現地工場においても、国内の工場と同様に、図面通りの高精度な製品づくりと、多品種に対応する柔軟性の高い製造フローを確立しております。材料の手配から加工、研磨、表面処理までの部品製作の一括対応に加え、試作品・多品種小ロット生産から量産品は当社にお任せ下さい。
解決の難しい課題ならお任せください!
MIM部品を中国調達に切り替えることでコストダウンを実現することができます。
|
海外調達による課題解決事例
用途 | タッチペン用金具 |
材料名 | SUS304 |
結果 | 中国広東省のMIM工場にて金型製作から生産まで一貫して対応。成型→脱脂→焼結→整形→熱処理まで対応。先端のプレス製品とはカシメ、ネジ締めして組立しております。MIM部品の量産コストを35%削減、金型制作コストは50%削減ができ、人件費・加工費が日本と比べて安価なので大幅にコストダウンすることに成功。 |
用途 | 美顔器用部品 |
材料名 | SUS316L |
結果 | 中国広東省の工場にて金型製作から生産まで一貫して対応。成型→脱脂→焼結→整形→サンドブラスト
試作コスト50%、金型の製作費用50%削減することができ、コストダウンに成功。 |
用途 | 医療機器 |
材料名 | SUS630 |
結果 | 中国広東省の工場にて金型製作から生産まで一貫して対応。成型→脱脂→焼結→整形→熱処理まで対応。金型製作から量産まで一貫して対応。また、一貫対応とノンストップ生産で納期短縮と量産コスト30%の削減に成功。 |
用途 | 医療機器 |
材料名 | SUS630 |
ダイキャスト(die-casting)で製作をしていたが、鋳巣が多く発生することから強度不足となり、組み立て後に割れが頻繫に発生。ダイキャスト(die-casting)からMIM(金属粉末射出成型)へ工法転換することで、工程内不良が減り、コストダウンへとつながった。 MIMは蜜度95% 以上で、空孔は丸い独立した形をとっているため、機械的強度が優れている。 |
用途 | 理容師用ハサミ |
材料名 | SUS316L |
中国広東省の工場にて金型製作から生産まで一貫して対応。成型→脱脂→焼結→整形→バフ研磨まで対応。従来ダイキャストで製作していた部品だが、巣穴の関係で磨き後に不良が多発。MIM化することで、歩留まりが大きく向上した製品に完成。 |
岐阜精器工業
TECH-JOURNEY
金属・樹脂加工の海外調達、コストダウンなら